Contents
- 1 7 Steps for the manufacturing of Concrete
- 2 1.BATCHING
- 3 2.MIXING
- 4 3.TRANSPORTING
- 5 4. PLACING
- 6 5. COMPACTING
- 7 6. CURING
- 8 7. FINISHING
- 9 FAQs related to Manufacturing of Concrete:
- 9.1 Q1: What are the main materials used to make concrete?
- 9.2 Q2: What is the ratio of concrete?
- 9.3 Q3: What are the basics of concrete?
- 9.4 Q4: What are the 5 types of concrete?
- 9.5 Q5: What is the strength of concrete?
- 9.6 Q6: What is concrete density?
- 9.7 Q7: What is the unit of concrete?
- 9.8 Q8: What are the chemicals in concrete?
- 10 Conclusion
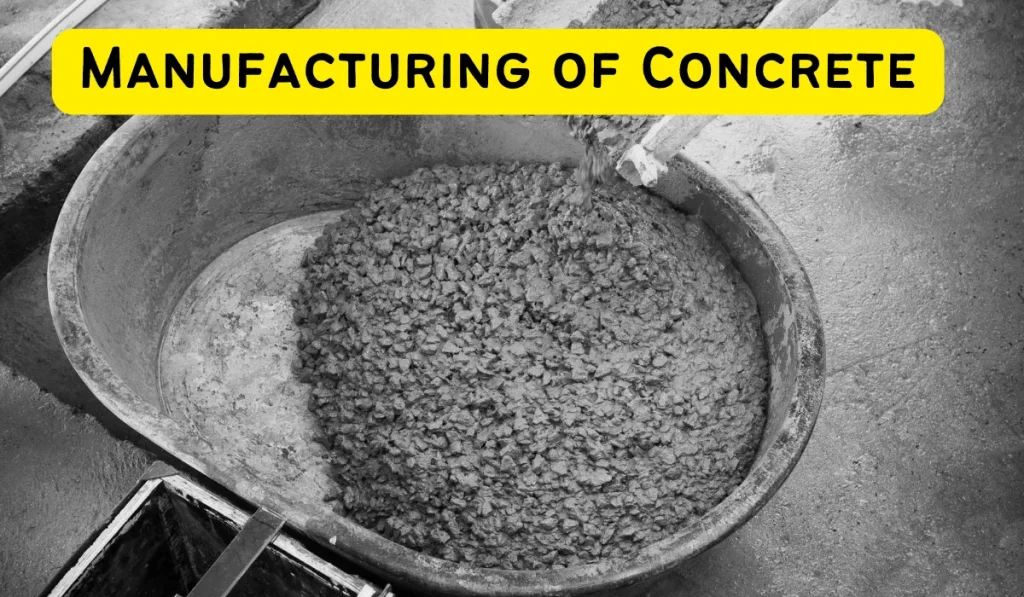
Manufacturing of Concrete is the process of mixing aggregate with cement and water to produce a concrete mixture. Then, the mixture is poured into a formwork where it hardens into a solid mass, which can be used for a variety of applications.
There are many reasons to consider concrete as a viable option for construction. More and more people are realizing that concrete is indeed an eco-friendly material that is cost-effective. This blog post will primarily focus on the manufacturing of concrete. Manufacturing of concrete is in following sequence of operation:
7 Steps for the manufacturing of Concrete
Part of the construction process is the manufacturing of concrete. The manufacturing of concrete is an involved process, but one that is necessary at this point in time. There are a few steps that need to happen before the manufacturing process begins.
Below down are 7 step by step guide for the manufacturing of concrete :
1.BATCHING
- The process of measuring the ingredients required for the preparation of the concrete is termed as ‘Batching’.
- Batching can be done by any of the following methods:
- Weight Batching
- Volume Batching
- Volume batching is generally not preferred as correction due to bulking is to be applied in this case.
- Volume batching is used only for minor engineering works only after the permission engineering incharge.
- Measurement of binding material, fine aggregate, coarse aggregate and water must be done with an accuracy of +/- 3% of batch size , and measurement of aggregates must be done with an accuracy of +/- 7% of batch size.
Now, suppose a site is using a concrete where the unit content of water, cement, sand and coarse aggregate are 180kg/m3, 360kg/m3, 700kg/m3, 1210kg/m3 respectively for a portion of work the engineer permits volume batching and rectangular box is measuring 35x45cm2 have to be fabricated to measure the coarse aggregate. Assume the following:
- The mixture available will mix the concrete with 2 bags of cement 150kg at one time.
- Two boxes of coarse aggregate will be used in a batch as defined above.
- When a field in a normal manner the void content is 40%.
S.G of C.A= 2.74, find the height of box=?
For 1m3 of concrete
W;C;S;G=1 ; 2 ; 3.89 ; 6.729 (by mass)
for 2kg of cement mass of gravel required=6.72
for 50kg of cement mass of gravel required=6.72/2 x50
=168kg
Volume of 168kg of gravel=168/2.75×103 =0.061m3
35x45xHx10-6x0.6×2(without air)=0.061
h=32.27cm
2.MIXING
- The process of obtaining the uniform color concrete of desirable strength is termed as “MIXING”.
- As per I.S 456 mixing time is 2min.
- Generally 20 revolution are sufficient to obtain the desirable mixing.
- With increase in mixing time up to 2 min compressive strength of the concrete is observed to be increased but increase in mixing beyond 2 min. It again starts reducing due to loss of water which takes place by the heat generated during mixing.
Mixing can be done by the following methods:
- Hand Mixing
- Machine mixing
Machine mixing is further sub-divided into two parts:
- Batch Mixing
- Continuous Mixing
And now, continuous mixing is also divided into two parts:
- Tilting type
- Non-tilting type
3.TRANSPORTING
- The entire process of mixing, transporting, placing, compacting and finishing must be completed in less than initial setting of the cement.
- Transporting of the concrete can be done by any of the following methods:
- PANS
- HAND BUGGIES
- POWER BUGGIES
- CRANE BUCKET
- TOWER BUCKET
- TREMIE CONCRETING
- DUMP TRUCKS (mass concreting)
- TRANSIT MIXERS
- CONCRETE PUMPS
- CHUTES
- BELT CONVEYORS
4. PLACING
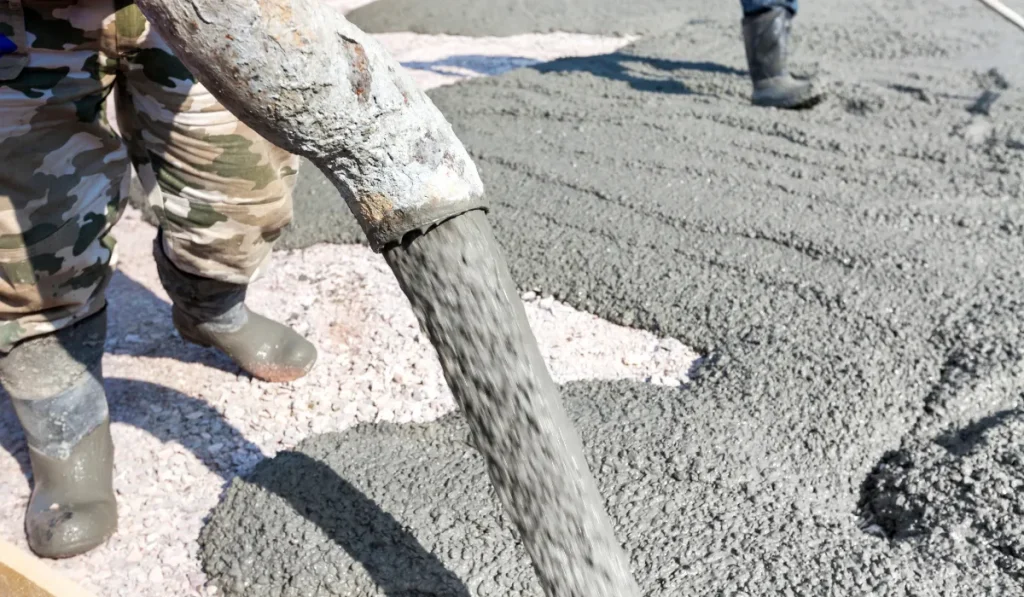
The process of the application of the concrete at the desirable location is called “PLACING” .
5. COMPACTING
The process of removing the entrapped air from the concrete and to form a homogeneous dense mass is termed as “COMPACTION”.
- If due to improper compaction done, if even 5-10% of air voids are left in concrete then strength of concrete is reduced by 30-60%.
- Compacting can be done by any of the following method:
- Hand rodding
- Pressure shock
- Centrifugation/Spinning
- mechanical vibration
6. CURING
- The process of preventing the loss of water added in concrete for hydration and to maintain satisfactory temperature regime is termed as “CURING”.
- Curing must be done at least for 7 days (However it is desirable for 3 weeks). At the temperature of 5-28oC and humidity of 90%.
- Curing can be done by any of the following methods:
- Shading of concrete surface.
- Covering of concrete surface with wet gunny bags.
- Sprinkling of water over concrete surface.
- Pounding of water over concrete surface.
- Accelerated curing (rate of curing, rate of hydration, infrared curing / steam curing) (Time of curing is less)
- Application of curing compounds (Acrylates, chlorinate rubber, sodium silicate (water glass),linseed oil, bitumen, wax) .
7. FINISHING
The strength of concrete depends upon both age and temperature of curing. This product of age and temperature of curing is termed as “Maturity of concrete”.
Q1: What are the main materials used to make concrete?
Ans: There are three main materials used to make concrete: aggregates, cement, and sand. Limestone and cement are the most common materials that are used for making concrete. Limestone is a type of rock, and it is the biggest source of cement. The sand is the third most common material used to make concrete.
Q2: What is the ratio of concrete?
Ans: . The ratio of concrete is the ratio of cement to aggregate. It is common to find a ratio of 2:1, but it can vary depending on the type of concrete that you are using. The ratio of concrete is also measured by weight or by volume.
Q3: What are the basics of concrete?
Ans: The basics of concrete are that it is a mixture of water and aggregate such as sand and gravel. The aggregate is what makes it hard and concrete. There are two types of aggregate that are most common in concrete mixes: sand and gravel. The sand is not just regular sand, but is a type of sand called “silica sand.” If a mix is too wet, it will be too soft and will not be able to support weight. To avoid this, the mix should be finely graded. If the mix is too dry, it will be too hard and may crack if it is overexposed to the sun.
Q4: What are the 5 types of concrete?
Ans: Concrete is a mixture of sand, gravel and water. It is used for construction, paving and for other purposes. The five types of concrete are: Portland cement concrete, lime-based concrete, ordinary concrete, high-performance concrete and geopolymer concrete.
Q5: What is the strength of concrete?
Ans: Concrete is a mixture of lime and aggregate that hardens when water and cement are added. Its strength is due to the hydraulic pressure generated by the addition of the water and cement. The strength of concrete is affected by the size of the aggregate particles used, the amount of water used, the amount of cement used, the type of aggregate, and the type of cement used.
Q6: What is concrete density?
Ans: Concrete density is 2.4 g/cm³
Q7: What is the unit of concrete?
Ans: The unit of concrete is the cubic meter.
Q8: What are the chemicals in concrete?
Ans: The chemicals in concrete can vary depending on the type of concrete. It is common for concrete to contain chemicals such as silica, alumina, aluminum oxide, and chromium.
Conclusion
Manufacturing of concrete is the process of preparing a mixture of cement, aggregate, and water to form a concrete product. It is the most widely used construction material in the world. It is produced in many places, but there are only a few major producers of concrete.
We hope you enjoyed our blog about the manufacturing of concrete. If you are interested in learning more about manufacturing concrete, we created this article for you. This article will tell you what concrete is and how it is manufactured. We also have some tips for choosing the best concrete for your needs. Please contact us anytime if you have any further questions by visiting EduKar.
Thank you for reading, we would love to hear from you!